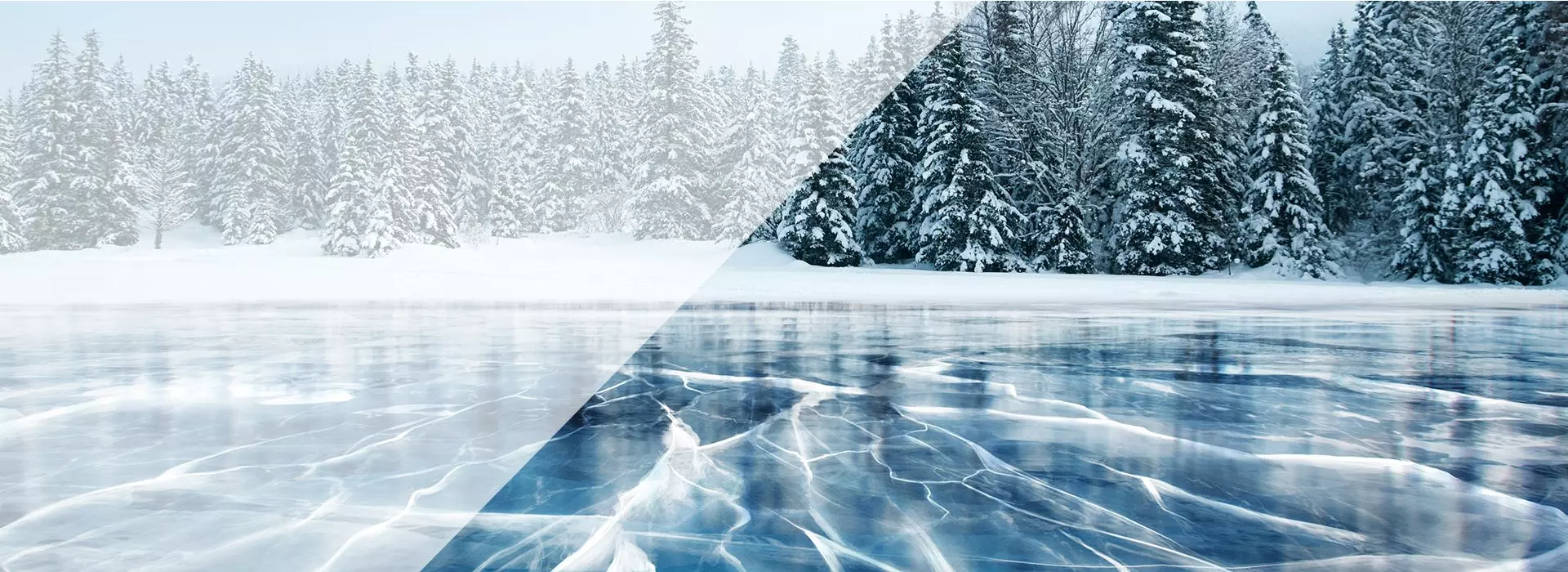
MORE SUSTAINABLE TECHNOLOGIES
Epson is committed to developing technologies that help customers achieve their sustainability goals and reduce carbon impact.
Environmental Technology Development
In addition to product-based R&D, Epson is focused on the development of new materials and technologies that help to reduce environmental impact. Guided by our principle that all innovation should be rooted in solving societal problems, our goal is open innovation — collaborating through partnerships to leverage our proprietary technologies, products and services. We are committed to the advancement of ground-breaking biodegradable and recyclable materials and innovations including biomass plastics and recycled powdered metals.
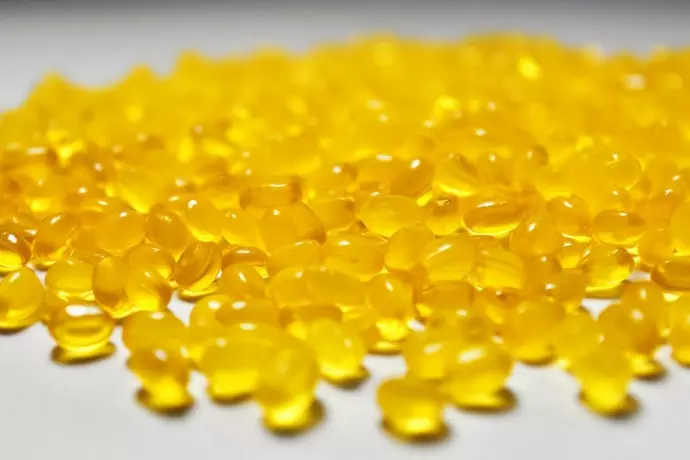
Biomass plastic
We are contributing to the development of a new form of bioplastic as part of a collaborative consortium of organisations. Pararesin is a promising biomass plastic that uses paramylon, a stored polysaccharide in Euglena algae. The consortium aims to have the capacity to supply approximately 200,000 tonnes of the marine-degradable, biomass-derived plastic annually by 2030 as a viable alternative to conventional plastics.
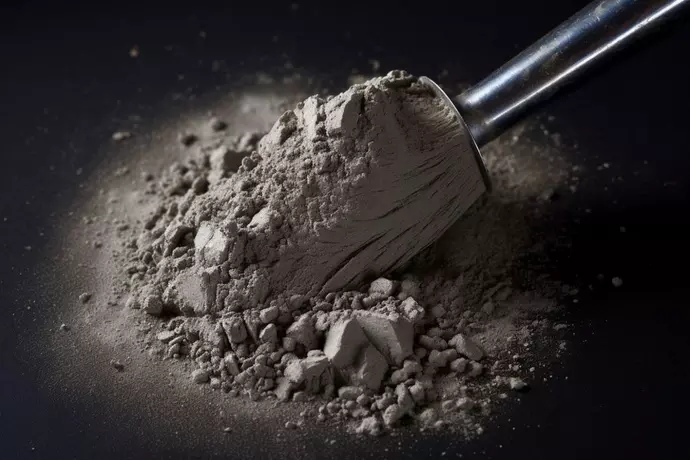
Powdered metals
We are working through our subsidiary company, Epson Atmix, to build a circular manufacturing infrastructure by creating products for 3D moulding using metal powders refined from waste metals that can be used to create components including car and electrical parts.
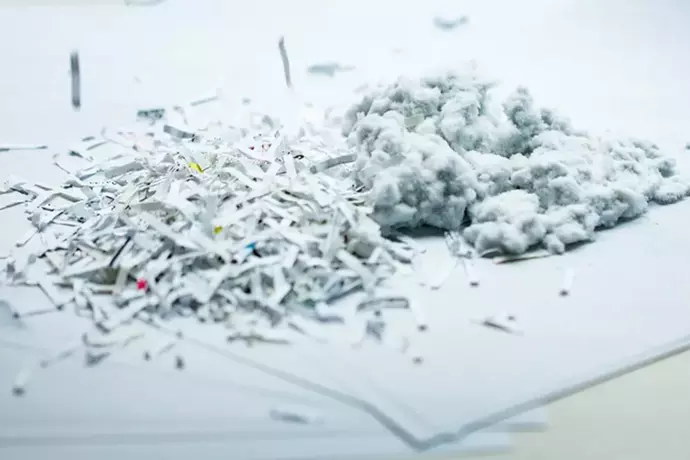
Dry fiber technology
Dry Fiber Technology is a proprietary set of technologies developed by Epson. It transforms fibrous materials into tangible value without using water by defibrating, binding and forming fibrous materials for different applications. We have named this type of manufacturing SmartCycle as it creates value from things that were once disposed of as waste and reduces the impact of manufacturing operations. One of the products that uses Dry Fiber Technology is Epson’s PaperLab, the world’s first office papermaking system, a machine that produces new paper from used paper without using water.
Printing Technology
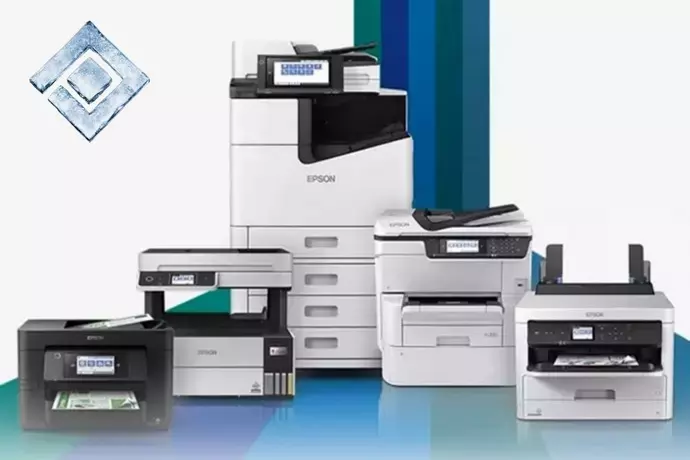
Office Printing
Epson Heat-Free inkjet printing technology is helping businesses to reduce energy usage. In comparison to laser technology, Epson inkjet printers use low power consumption, saving energy and costs.
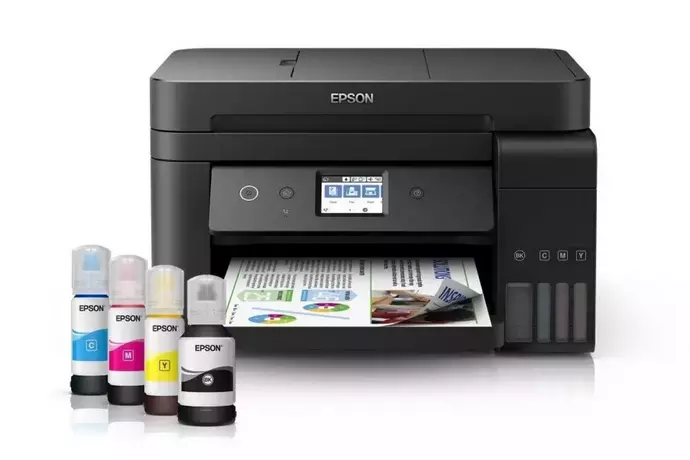
Home Printing
Epson’s cartridge-free EcoTank printer range is the more sustainable solution for home printing. It uses refillable ink tanks instead of cartridges – eliminating cartridge production, shipping, and end-of-life disposal. To date, we have sold over 90 million EcoTank printers worldwide, contributing to a significant reduction in the use of plastic, which is one of the main components of ink cartridges.
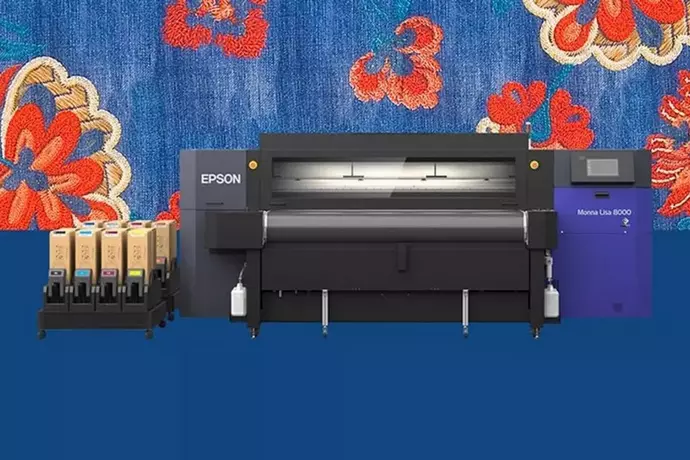
Textile Printing
Digital textile printing is playing a key role in the sustainable transformation of the fashion industry. When compared to traditional textile printing methods, digital printers such as Epson’s Monna Lisa drastically reduce water consumption. This means less wastewater is sent to treatment plants, and the amount of energy needed to heat water is reduced. Localising fashion using in-house, on-demand digital textile printing means a reduction in CO2 per item, as they are no longer shipped long distances and manufacturers avoid environmental issues associated with traditional dyeing processes.
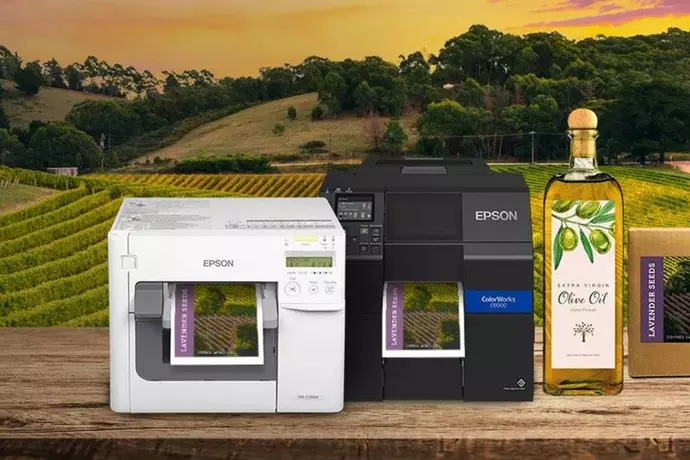
Label Printing
Independent research suggests that if European businesses switched to on-demand inkjet labelling, energy savings of 28.7 million kWh could be achieved each year – equal to a reduction of 6.7 million tonnes of CO2. They could also eliminate 180 million square metres of label waste, and cut ink waste by an estimated 619 tonnes.
Visual Communications Technology
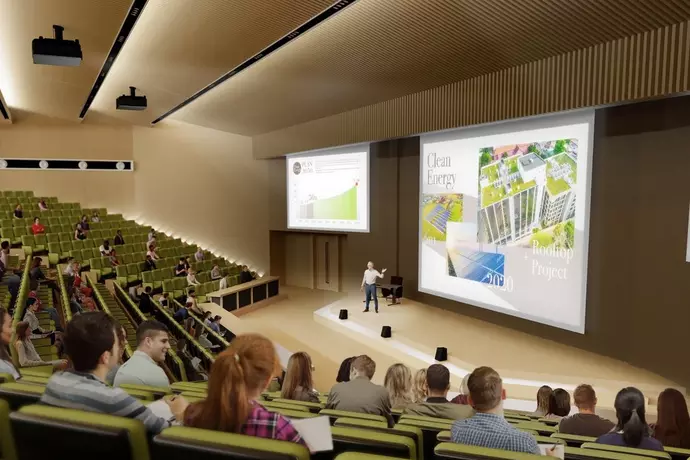
Projector Technology
We’ve developed the world’s smallest, lightest high lumens range of projectors. Environmental benefits of this new, more compact technology include lower power consumption, fewer resources to manufacture and reduced packaging requirements. Our ultra-short-throw projectors and visualisers are improving accessibility in the classroom and supporting virtual teaching methods.
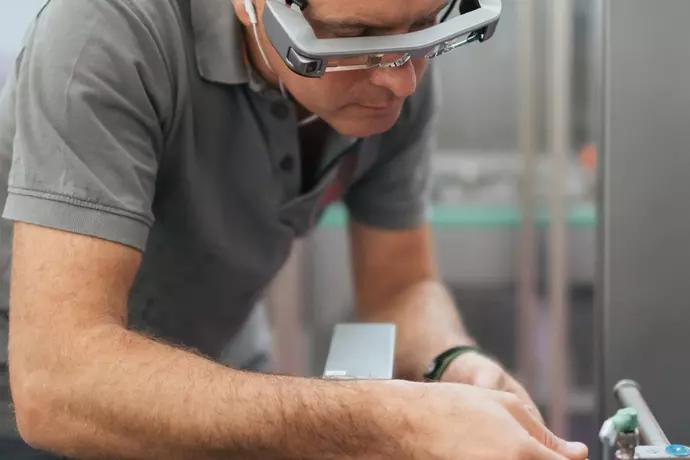
Moverio smart glasses
Epson’s Moverio augmented reality (AR) smart glasses have been developed for industrial applications in remote assistance, workflow guidance, and training. These applications significantly reduce the need for long-distance travel and face-to-face contact, with additional benefits such as faster response times, higher first-time fix rates, increased productivity, reduced travel costs, and associated CO2 emissions.
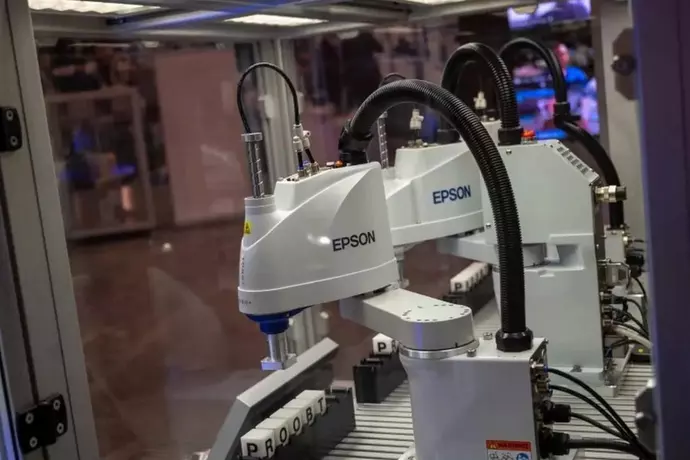
Manufacturing solutions
The pandemic highlighted European dependency on Far East production. Increased demand for more localised automation (reshoring) is reducing reliance on carbon-heavy offshore production. As the world’s leading manufacturer of SCARA robots, Epson has seen significant demand by SMEs based in EMEAR and, to support this demand, we have developed robotic manufacturing solution software to help smaller companies in setting up localised production lines.
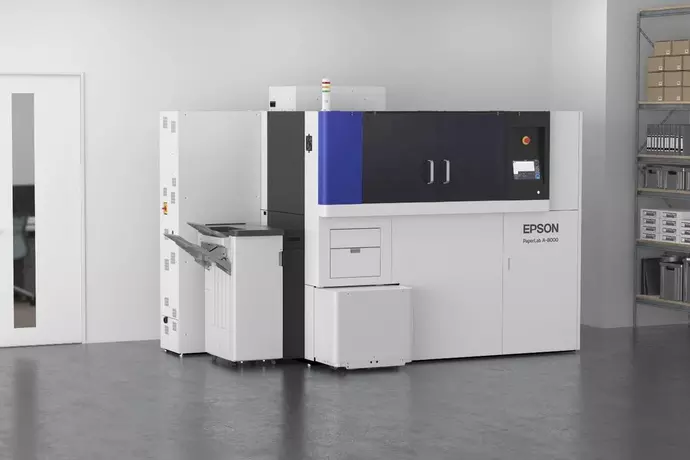
PaperLab
Offices are giving rise to growing volumes of paper waste, which represents over 50% of a business’s total waste, and comes with an increasing carbon footprint. It is estimated that paper accounts for over a quarter of total waste at landfills and around 42% of global wood harvest.
PaperLab is the world’s first in-office waterfree secure paper recycler, which enables organisations to recycle and upcycle paper in one process. It offers a truly circular solution that significantly reduces paper, water usage and carbon emissions.
Based on Epson’s innovative Dry Fiber Technology, PaperLab can produce up to 720 A4 or 360 A3 sheets of paper each hour. It also provides an onsite solution to removing or destroying sensitive information, which is often contained on paper waste. Carrying out this process offsite can result in risks, higher costs and carbon output – all can be sidestepped once genuine circular principles are implemented.
Discover more about sustainability at Epson
1 Sustainability in Labelling, May 2021; Smithers Report
2 Calculated using standard conversion of 0.233kg of CO2e per kWh of electricity.